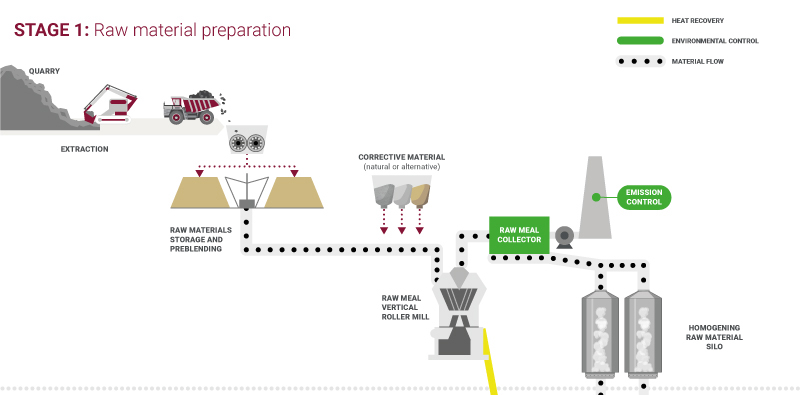
STAGE 1 – RAW MATERIALS PRODUCTION & PREPARATION
Mining or sourcing different raw materials that could be either natural resources (such as limestone, clay, shale, etc..) or alternative resources to produce a suitable dry powder called raw meal composed of defined proportions of Calcium (C), Silica (S), Alumina (A), Iron (F) to feed the kiln.
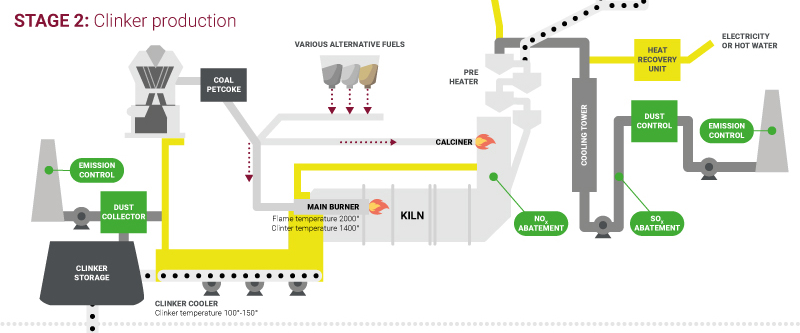
STAGE 2 – CLINKER PRODUCTION
Heating the raw meal to evaporate water, decarbonate and form the main components of clinker (C3S, C2S, C4AF, C3A)
- Heat is produced by a fuel mix composed of traditional fuels and permitted alternative fuels (a cement kiln is specifically appropriate for alternative fuel usage due to very high combustion temperature, sufficient retention time and ability to capture mineral part in the clinker)
- Before being stored, clinker is cooled down done to secure its hydraulic properties as well as to recuperate energy to feed back in the kiln process
- Heat recovery is maximized for internal use (e.g. drying raw materials or fuels) or external use (e.g. electricity or hot water for local community)
- Gas emissions are controlled on a continuous basis with abatement of relevant components (SO2, NOx, HCl, dust, etc…) whenever necessary.
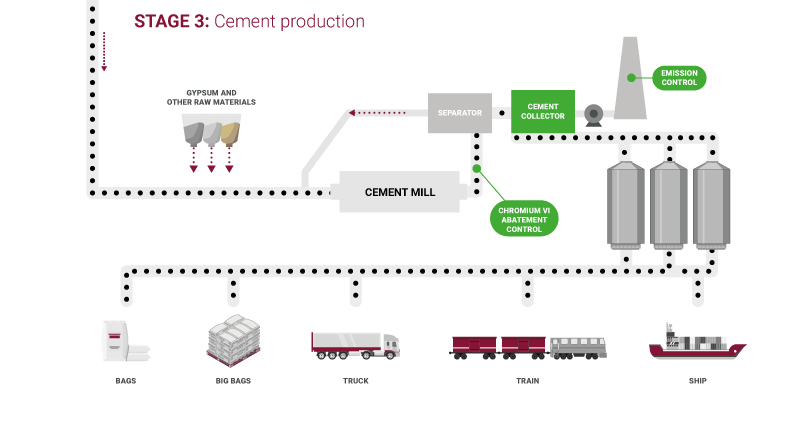
STAGE 3 – CEMENT PRODUCTION
Mixing and grinding clinker with other raw materials (gypsum, slag, fly ash, pozzolana, calcined clay, limestone...) depending on cement types at adequate fineness to reach the desired cement characteristics (strengths, expansion, color...)
QUALITY CONTROL
is done on all input materials & fuels, at every step of the process, on clinker and cement